Exclusive: Could nanobots transform Australian mining?
By Nurfilzah Rohaidi
Interview with mining futurist Gavin Yeates.
The mining futurist believes that a more sustainable approach to mining will include “swarms of nanobots”, burrowing deep into the earth and targeting valuable minerals. “You extract them with a mechanical device that is incredibly small, and we’re talking at molecular scale,” Yeates explains.
In an energy-hungry industry, this focus on “specificity” could use less energy and produce less waste, he tells GovInsider on the sidelines of the 3DEXPERIENCE Forum Asia Pacific South 2018 in Adelaide, South Australia last week.
Targeted mining
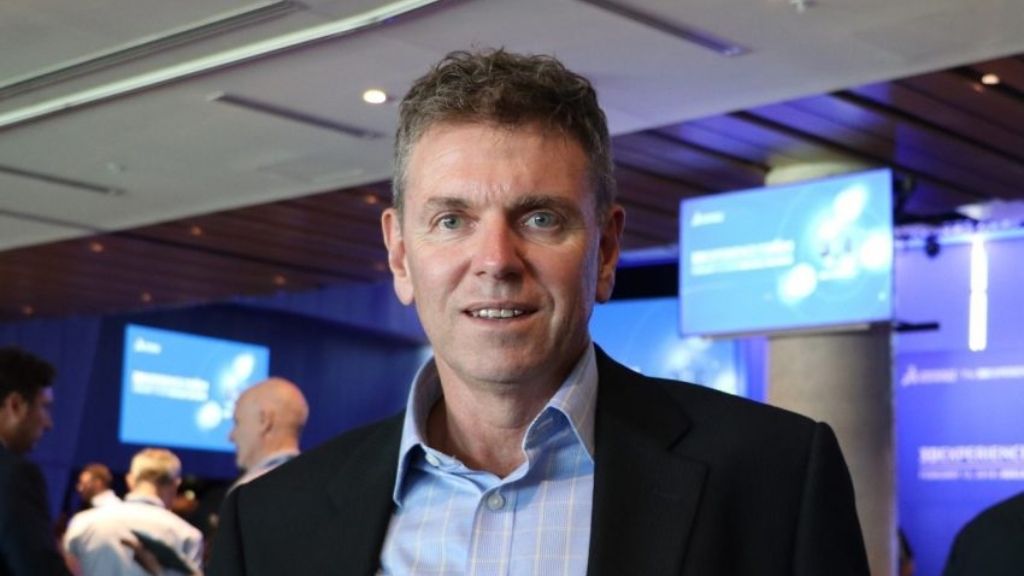
Yeates’ role as a mining futurist includes helping mining organisations to harness data, sensors and other types of technology to develop “totally new ways of extracting” that are more productive and less impactful on the environment.
The traditional mining process goes like this: drill holes into rock; blast them to pieces with explosives; shovel up these pieces into trucks; and transport them to grinding mills, he explains.
His vision for digital transformation in mining involves “smart, intelligent, mini-, micro-, nano-machines” that will lead to lower costs, more sustainable methods, increased safety, and a “massive improvement in productivity”.
For instance, Australia’s scientific research organisation, the Commonwealth Scientific and Industrial Research Organisation (CSIRO) is currently developing methods where fluids are injected into the rock, effectively dissolving the target mineral and making it easier to extract, Yeates says. But there are minerals that cannot be dissolved chemically—which is where nanobots come in.
The point is to ensure that the nanobots only extract the mineral, leaving the surrounding rock behind. “Our current methods include taking the seam of mineral plus a whole lot of waste around it, and we spend a lot of money crushing and grinding that waste,” he explains. Nanobots such as these could be a reality in as little as 20 to 30 years, he adds.
CSIRO is also developing technology that turns hazardous waste into power that can be used to power operations at the mine, reducing methane emissions along the way.
Looking beyond the horizon, Yeates predicts that mining companies will move towards “customisation” and scaling of equipment. If the seam of mineral in the ground is only a few metres wide, that is a compelling reason to develop extraction equipment that is that particular size, he notes.
Extraction by remote control
There is also potential for driverless vehicles to transform the mining industry. 200 autonomous trucks are already operating in the world today, “most of them in Australia”, according to Yeates.
In Pilbara, Western Australia, blast hole drilling and most other operations are already being done remotely. The most important benefit here is that it makes these dangerous tasks safer for miners. “That’s not the future - that’s now,” Yeates remarks.
This means that the trucks that transport the mined material can also be customised. “If you don’t need an operator to drive it, we can rescale them to whatever size makes sense,” he points out.
“If you don’t need an operator to drive it, we can rescale them to whatever size makes sense.”Sensors in various parts of the mines could provide real-time data that enriches operators’ understanding of the orebody in the ground. They will be able to simulate different scenarios of processing for each ore type, and identify “which bits are valuable, and reject the bits that aren’t”, Yeates says.
This wealth of data allows companies to gain insights into performance, and carry out predictive maintenance. Mining giant BHP Billiton, where Yeates spent 35 years previously, is currently collecting and analysing data from their trucks all over the world to do just that, he explains.
From old to new
Mining “hasn’t changed” in almost a hundred years, says Yeates, who is a board member of the Australasian Institute of Mining and Metallurgy.
“We have been able to increase the scale so our equipment is bigger, but the fundamental technology behind them hasn’t changed,” he notes.
Furthermore, each step in the process is managed in a siloed way, where “each is being optimised, but not together as a whole”. “It’s not going to be sustainable long-term, so we have got to do something different and push for a step change,”
Yeates says. He intends to drive change in this very traditional industry, as digital can be a “pretty significant lever to value”.
And as the industry transforms, he hopes to see governments do their part to support mining companies, particularly on the research and development side. Much of modern life hinges on the commodities produced by mining, and for emerging countries in Asia, “the impact of mining can be significant on their economies and growth in GDP”.
Mines could look very different a decade or two down the road. Machines and robots of all sizes will zip around, doing the heavy lifting or digging into the earth, with humans giving commands a safe distance away.
This is the mine of the future - and with the pace of change today, it may come faster than you think.