How assembly lines inspired Asia’s hospitals
By Medha Basu
Technique helps Malaysian hospitals cut waiting time by more than half
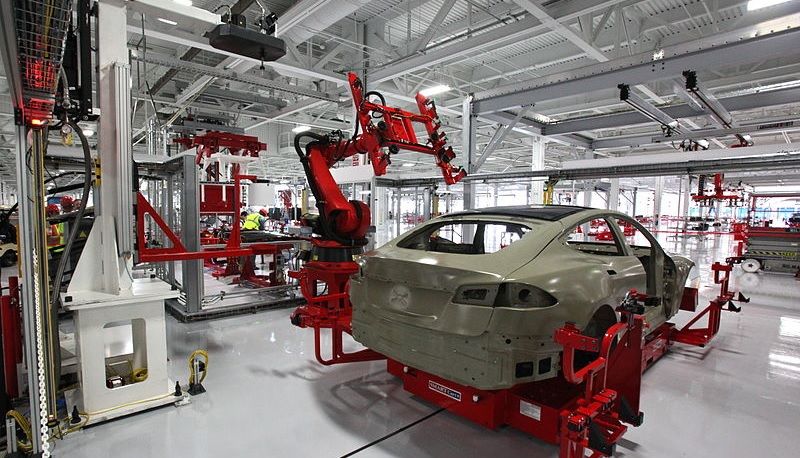
Hospitals across Asia have adopted approaches first used in Japan’s car factories. As a result, a hospital in Malaysia managed to cut its waiting times in half.
This technique is called “Lean” management, and GI briefly explains how it works in healthcare.
How it works
Lean management asks all parts of an organisation to join in finding efficiencies and cutting waste. It was pioneered by Toyota after the Second World War, when Japanese industry was desperate to find any and every advantage in order to rebuild.
The central principle is that staff are constantly looking to remove wasteful processes. Could a set of spanners be next to each employee, for example, rather than on a workbench five metres away.
The broad technique has been adopted by hospitals. Take India’s Narayana Hrudayalaya Hospital, set up by cardiac surgeon Devi Shetty. Using lean practices, Shetty has dramatically increased the number of heart surgeries performed, almost like a car assembly line.
“Shetty and his team of forty-odd cardiologists perform about six hundred operations a week in a veritable medical production line. No Western hospital comes close,” the book The Fourth Revolution notes.
Doctors’ performance is measured by the time they take per surgery, the number of stitches they use to close up, and the amount of blood replaced through transfusion. Through focussing on these efficiencies, more patients can be treated - more lives can be saved.
Results in Malaysia
Malaysia piloted the technique in Sultan Ismail Hospital in 2013. Its orthopaedic clinic, which previously operated from 8am to 5pm, was able to clear patients by 2:30pm on most days. “We use lean management techniques to remove bottlenecks and focus on the speed at which processes are completed,” wrote Idris Jala, CEO of Malaysia’s Performance Management and Delivery Unit, in his Transformation Unplugged blog.
For instance, a simple step like getting the next patient in line to wait outside the doctor’s door helped save time. The hospital’s oncology unit cut queues for radiotherapy from four months to one month for head and neck cancer patients through simple changes.
The government is now expanding the technique, planning to eventually cover all 14 state and 133 government hospitals.
Also being implemented outside hospitals. Malaysia is testing the approach to acquire land for agriculture, Jala wrote. Acquiring land for irrigation can take almost two and half years, and it plans to shorten this to 11 months.
Any downsides?
There could, however, be downsides of the technique. Setting efficiency targets could encourage the wrong behaviour from employees. For example, they could focus on efficiencies at the expense of patient care. A patient might be treated faster, but if something is missed because they weren’t asked enough questions, they may have to return.
Equally, if lean techniques are not introduced correctly, they can demoralise employees. For example, when the British tax office introduced it, employees went on strike. They assumed it was being used to find evidence to make job cuts.
But lean is intended to be a supportive, inclusive process. It tells every employee that their view is valued. Rather than management consultants or senior figures guiding an organisation, everyone has a say in how to improve operations.
The lean management technique was first used on Japan’s factory floors. But today it is being used from India’s operating rooms to Malaysia’s paddy fields. The stats show that it seems to be working.