Exclusive: Singapore plans for construction robots
By Vanessa Gu
How the Building and Construction Authority is going for a digital push.
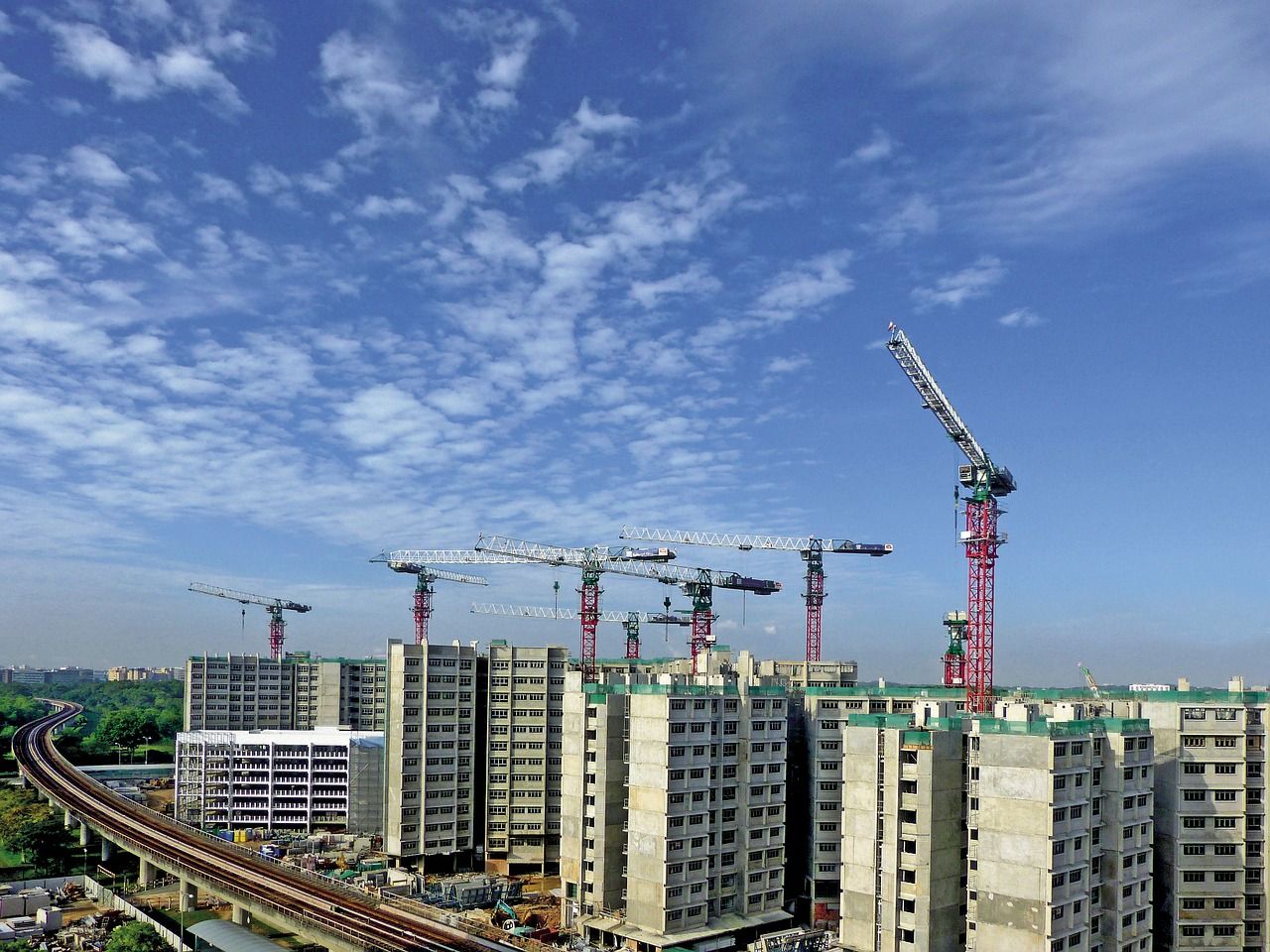
Robots will do the heavy lifting, while autonomous cranes and excavators will pepper construction sites in 2050. This is the future Cheng Tai Fatt paints as he sat down with GovInsider to talk about digitalisation in the construction sector.
Cheng gives us an inside look into the Building and Construction Authority’s(BCA) digitalisation plans, and how that will shape the future skyline of Singapore.
Robots: The future of construction
Singapore relies heavily on foreigners in its construction industry, and with an ageing population, the government will want to look at using less labour and increase productivity in the sector. While technology has not matured to the extent where construction robots can run autonomously, Cheng believes that “some of these robotics can also carry materials, payload on-site, or in the factory”.
3D printing is the next thing that’s on the horizon for the building authority. Nanyang Technological University unveiled a 3D printed toilet earlier this year, Cheng notes, and the BCA is considering whether it can be scaled up, or “whether you can do it on the larger economy of scale.” Meanwhile, a US$107mn centre is testing how 3D printing can be used to build public housing.
‘Lego’ construction as the norm

Singapore unveiled the world’s tallest modular building project this year - two 40-storey residential towers, where 65 percent of it were constructed using pre-fabricated blocks, according to its builder. This is a trend BCA is hoping to follow, especially with a manpower crunch in Singapore, says Cheng.
The move to pre-fabricated buildings also gives more room to deploy new technologies. “If you're under a manufacturing environment, then there is scope for you to do more robotics, do more automation,” Cheng explains. Instead of checking the quality of buildings as it is being built, defects can be fixed before blocks are even out.
In a crowded city like Singapore, this mode of construction can also reduce inconvenience to people around, he says. With modular buildings, “they shift it there in blocks, and they just plug it on site,” and Cheng continues that “residents nearby don't even notice - because there is almost no noise."
Digital twins for buildings
Data will underpin BCA’s vision for the future. It will plug information gaps in the construction process by consolidating all data from the design, construction, and operation processes on a single platform. This will enable builders to make data-driven decisions at all stages of a building’s life cycle and also minimise abortive work.
A key part of this transformation is having a digital twin for every physical building, so what happens physically is also reflected digitally, he says. The immediate access to data on how a building is performing “can be used to manage your buildings, and the operation and maintenance,” Cheng says.
The plan will also help build smarter and greener buildings. Sensors will be able to monitor things like energy-use and leakages for more efficient use of resources and timely maintenance. With better connectivity between the built environment and sensors, “you will have real-time information,” and Cheng continues that “if you capture a lot of data, you can do some predictive analysis.”
Construction is still a labour-intensive sector in Singapore, and Cheng acknowledges that it has been slow to adopt new technologies. With BCA’s vision, however, Cheng hopes a more digital construction can reduce manpower needs and build smarter buildings for the ever-evolving city.