Tabitha Quake, Assistant Head and Senior Prosthetist/Orthotist, Foot Care & Limb Design Centre, Tan Tock Seng Hospital, Singapore
By Sean Nolan
Women in GovTech Special Report 2021.
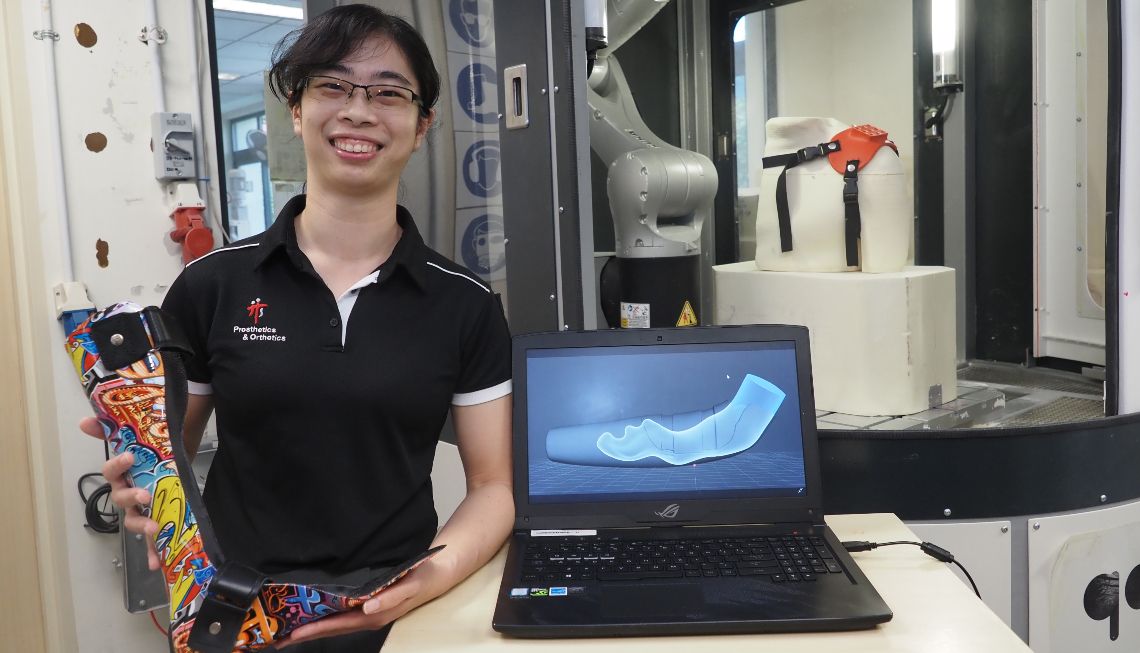
As the Assistant Head of Tan Tock Seng Hospital’s Prosthetics and Orthotics Service, I lead a clinical and technical team of Prosthetists/Orthotists and Technicians to provide customised prostheses (artificial limbs) and orthoses (braces/splints for the spine and limbs) for patients with limb loss or who suffer from neuromuscular conditions affecting their mobility.
Prosthetists and Orthotists (P&Os) are allied health practitioners trained in the prescription, design, manufacture and fitting of customised prostheses and orthoses. Under the banner of the Foot Care and Limb Design Centre, which houses Singapore’s pioneer services for limb design and podiatry under one roof, we have had the privilege of providing integrated and innovative care solutions for the nation for the last 40 years. Our P&O Service draws on the latest in prosthetic and orthotic technology to provide individualised adaptive solutions for patients.
Since 2016, the Service has made significant inroads increasing our digital footprint, applying a range of digital shape capture and manufacturing technologies to our customised device line-up. Digitally captured and rendered 3D models enable us to manufacture customised devices with greater speed, accuracy and quality compared to our conventional, manual processes.
Today, our range of digitised services and products includes 3D scanning and design rendering for lower limb and spinal orthoses, silicone prosthetic covers, and orthopaedic footwear. We have also tapped on additive manufacturing technologies in 3D printing to produce bespoke ankle foot orthoses (AFOs) and upper limb prostheses for our patients.
What was the most impactful project you worked on this year?
This year has been a milestone for the Service in the way of incorporating a User Centred Design (UCD) approach into our clinical practice through a series of individual use cases. Traditionally, healthcare practice has been, and is still very evidence-based. Healthcare outcomes and services are still largely viewed from a clinician-centric, prescriptive perspective.
In contrast, UCD seeks to understand what end users, in this case, the patient, values and requires of the end-product, and involves them throughout the product development process. The capability of digital design technology and additive manufacturing methods to rapidly generate functional prototypes, which can be fine-tuned to incorporate user feedback into subsequent iterations, lends itself well to this interactive, high-touch design approach.
This allows patients and clinicians to collaboratively design and derive unique and personalised solutions that are of value to the end user. Digitalisation of our clinical processes, combined with a greater emphasis on user experience through UCD, has enabled P&Os to design and create adaptive devices that do not conform to traditional design envelopes of prosthetic/orthotic devices.
In collaboration with service designers and engineers from TTSH’s Centre for Healthcare Innovation’s Living Lab (CHILL), makerspace, this series of use cases has seen us create a variety of unique and highly personalised devices, ranging from adaptive sports equipment, an arm ortho-prosthesis, and adaptive devices for personal functions. Leading the team through this novel approach to care has been a learning journey, as we bounce ideas off one another and challenge tried and tested ways of doing things.
Involving patients as co-designers, rather than passive recipients of care, and actively seeking their opinions and feedback on design was definitely challenging for the team, who is by training accustomed to doing the designing. Through the frank conversations and active engagement between P&Os and patients that resulted, I saw a new level of buy-in and co-ownership of care from the patients, and saw my team invigorated by a second creative wind.
Seeing the fulfilment and satisfaction of both P&Os and patients as they reaped the shared fruits of their labour in bringing an idea from conceptualisation to end product, made me realise how impactful small shifts in our attitudes towards care and design can be.
What is one unexpected learning from 2021?
We often tend to think of digitalisation and human touchpoints as two opposing poles. However, our exploration of UCD has shown that digitalisation and the human touch are not mutually exclusive. Digitalisation and technology should not be viewed primarily as solutions, but as enablers. In the P&O context, digitalisation can introduce a degree of empathy and personalisation that may not be achievable through conventional processes. It can also help create high connectivity environment in which users are both highly involved and engaged over shared experiences.
What’s your favourite memory from the past year?
What drew me to the P&O profession was the profession’s drawing on resources in innovative ways to create niche, yet tangible solutions that had a positive and practical impact on others. The uniqueness and variability of the UCD use cases in the past year have led others to comment that P&Os can really “make anything”. The realisation that with the plethora of digital tools at our fingertips, we are starting to move beyond being simply “fixers” and solution providers, but to being makers and creators of possibilities, has been one of my favourite memories from the past year.
What’s a tool or technique you’re excited to explore in 2022?
I am looking forward to continuing to tap on digital technology in its various forms to not only expand the profession’s creative and technical capabilities, but to also incorporate service design and user experience aspects to our prosthetic/orthotic devices. The UCD approach will be pivotal to understanding what our patients value from not just their customised prosthetic/orthotic devices, but also from our services.
Computer Aided Design-Computer Aided Manufacturing (CAD-CAM) technologies in 3D shape acquisition, scanning, design rendering, as well as additive manufacturing technologies will form the technological backbone supporting our user-centred approach to service delivery.
What are your priorities for 2022?
With the shifting emphasis towards greater user-centeredness in the design of healthcare services, in the upcoming year, our Service will be spearheading research in tech-enabled care initiatives with a greater focus on user experience. We will be looking at harnessing the advantages of the latest in 3D printing technology to improve and optimise the design of our 3D printed AFOs to enhance our digital capabilities.
We are also foraying into new territory through the piloting of a remote-digital service delivery model for transtibial prosthetics, in collaboration with our inter-institution partners at Khoo Teck Puat Hospital and cross-industry additive manufacturing partner based in Europe. Through these initiatives, we hope to improve the accessibility of a niche segment of technology to our patient population, as well as improve accessibility and right siting of care for P&O services at a national level.
Who are the people who inspire you?
I believe inspiration can come from unexpected places, as long as one keeps an open mind. I am privileged to have mentors who encourage me to challenge existing pre-conceptions and think further and deeper about issues both clinical and beyond. My peers are also invaluable sounding boards for bouncing off and refining ideas together.
What gets you up in the morning?
Knowing that there are new challenges that demand creative yet practical solutions, and that the solutions I create can bring about impactful change is what gets me going each day.