The Philippines bets on 3D printing to supercharge industry
By Yen OcampoYogesh Hirdaramani
The Southeast Asian country’s Department of Science and Technology is turning to 3D printing to support industry players and supercharge its manufacturing sector.
-1717033028484.jpg)
‘Dr. Jose P. Rizal: The Filipino Scientist’ is the first and tallest 3d printed statue of the Philippine national hero. The 12.5-foot statue is made from acrylonitrile styrene acrylate (ASA), one of the research and development initiatives of the AMCen, under the DOST-Metals Industry Research and Development Center. Image: MIRDC
When someone fractures their ankle, there is a chance that their doctor may choose to use a bone graft to stimulate healing – but bone grafts can go wrong and are often expensive. This is why medical researchers in the Philippines are experimenting with using 3D printing tech to craft precise bone scaffolds that can encourage healing.
This is one of the many ways in which the Southeast Asian country is leveraging 3D printing, also known as additive manufacturing, to drive innovation. 3D printing has also been credited with supporting the country’s pandemic response, as leaders tapped on it to supply gaps in medical devices and personal protective equipment.
Now, the country’s Department of Science and Technology (DOST) is driving the adoption of 3D printing and similar advanced manufacturing tools through the Advanced Manufacturing Centre (AMCen). The centre was launched in 2021 to drive the adoption of cutting-edge tech to boost productivity, reduce waste, and improve product quality.
Enabling industry access to 3D printing technologies
AMCen aims to help industry, academia, and other stakeholders access 3D printing technologies, shares Engr Robert O Dizon, Executive Director of the Metals Industry Research and Development Centre (MIRDC).
These include 3D printing high-performance materials such as high-strength polymers, composites, metals, and ceramics.
“Through its provision of cutting-edge technologies and research and development support, AMCen drives innovation across industries, leading to the creation of new products and solutions,” says Dizon to GovInsider. Dizon shares that AMCen will be establishing satellite labs across the Philippines to provide technical services to industry players.
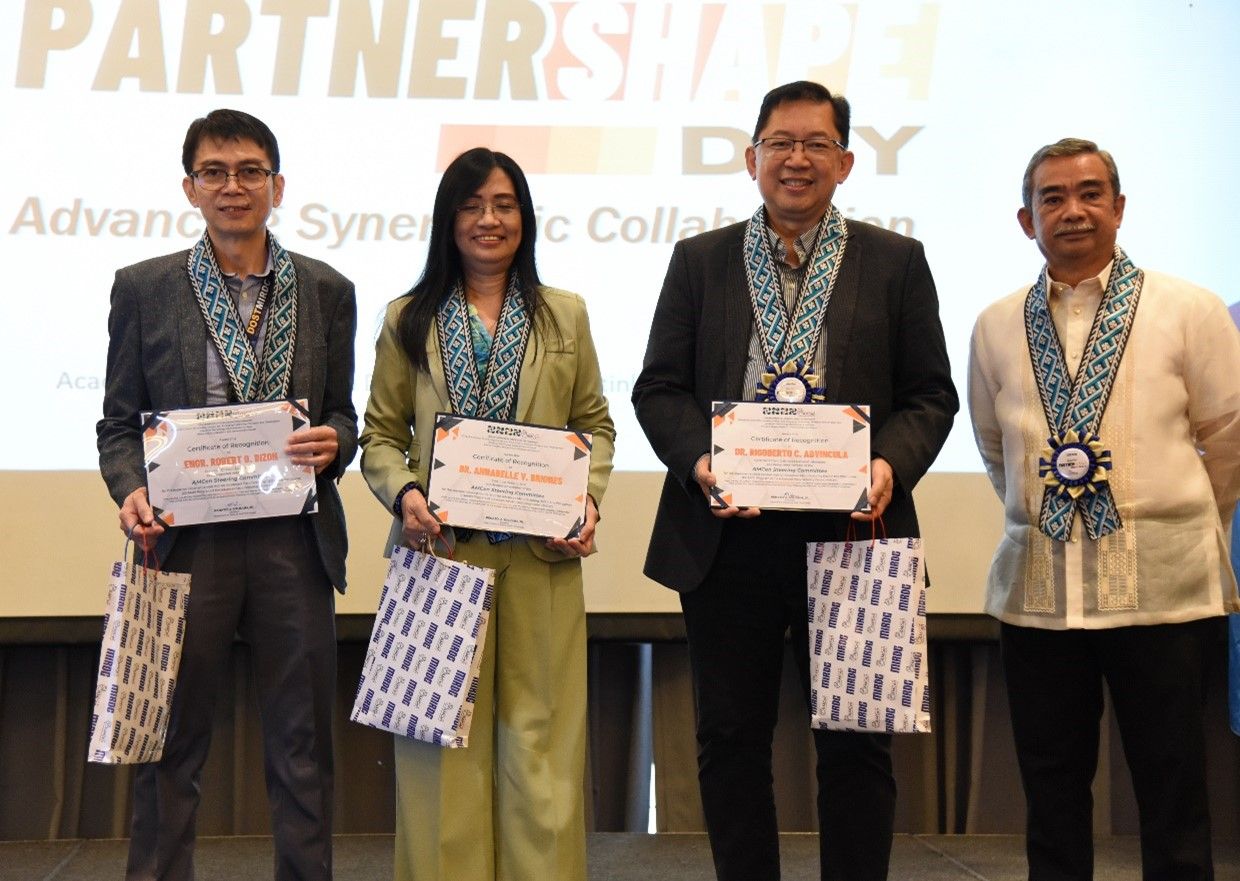
Advanced manufacturing is a key priority for DOST, which has allocated PHP 330 million (US$5.6 million) for AMCen’s 3D printing project, named the Rapid and Advanced Prototyping for Product Innovation and Development using Additive Manufacturing Technologies (RAPPID-ADMATEC).
DOST is also supporting the growth of other advanced manufacturing projects through the Industrial Technology Development Institute (ITDI), another R&D institution, which runs tech transfer and training programmes to support the industry.
“Promoting advanced manufacturing techniques improves productivity and efficiency, contributing to overall economic productivity gains,” Dr Annabelle V Briones, Director of ITDI, says.
According to World Bank data, manufacturing contributed approximately 18% of the country's GDP from 2018 to 2022.
3D printing in practice
Daniel Flores, Lead Mechanical Design Engineer at Line Seiki Philippines, Inc., has tapped on 3D printing to transform their product development process.
Before adopting 3D printing, the company faced challenges including lengthy lead times and high costs to create prototypes and custom parts. This hindered their ability to swiftly respond to customer demands and iterate designs efficiently.
Today, they can swiftly fabricate new product prototypes, evaluate existing quality issues, and produce parts in low volumes. The company can produce prototypes within a month, a fraction of the time previously required, explains Flores.
“The impact has been profound, with significant reductions in development time, lead times, and costs, as errors are minimised from the outset,” Flores says in conversation with GovInsider.
Despite challenges like precision and surface finish, Line Seiki remains optimistic about the future of 3D printing within their company. For example, Flores highlights that they could further use the tech to refine precision and strength, reduce printing costs, and replace parts with printed alternatives.
The company is also providing hands-on training for engineers and using 3D-printed parts as educational tools.
Shaping the future
While strategic institutions such as AMCen and ITDI are supporting industry players in adopting new technologies and skills, educational initiatives are playing a critical role in helping youth pick up advanced manufacturing skills.
Briones explains that 3D printing innovations will not only foster entrepreneurship but also create new economic opportunities and jobs. As the demand for skilled professionals grows, the government will continue to support skills development and education initiatives to ensure a capable workforce.
For instance, AMCen has developed five training modules, rolled out a National AM Curriculum, and piloted specialised courses for BS and MS students who wish to pick up such skills.
Similarly, the Integrated School of the University of the Philippines is rolling out the National Additive Manufacturing Curriculum for its second batch of students.
AMCen personnel themselves have been upgrading their 3D printing skills, having recently completed a study trip to the US to learn more about the role of 3D printing within construction.
For Dizon, 3D printing will continue to drive innovation within the Philippines, particularly in sectors such as aerospace, automotives, healthcare, electronics, and consumer goods. Briones similarly adds that 3D printing can enable sustainable manufacturing practices and green growth.